History Of Safes
In centuries past, humankind worshiped fire because they feared it. They saw it ravage palaces and dwellings with devastating results. So much of the written records of early human civilization are gone because of the lack of protection of these documents.
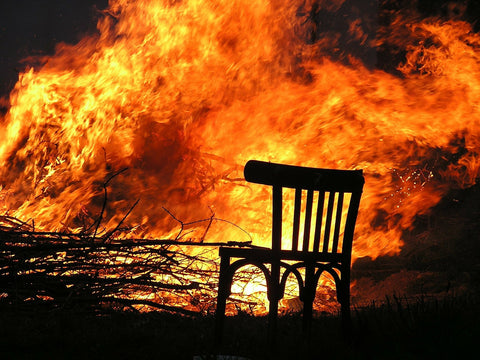
Through the ages, humankind has sought to protect their possessions from the terror of fire. The Egyptians buried their scrolls deep in the pyramids. The Assyrians buried duplicates of important documents at separate locations. The Greeks carved their important records on ivory slabs.
When no record material proved suitable for protection against the destruction by fire, they turned their talents to the development of protective devices to house records. Julius Caesar filed his records in strong, iron boxes but found that the metal readily conducted the heat of a fire. Feudal lords build underground vaults and stationed trusted guards for their protection. Merchants of the 15th Century developed the treasure chest of pirate story fame, made of oak and banded with iron.
After 1830 came the iron “safes” with inner walls of stone, plaster, wood, cement, brick, asbestos, mica, alum, chalk, clay, or simply dead-air space.
The first standardized tests for the adequacy of safe protection were not made until 1917, however. These tests caused radical changes in safe construction because they proved many of the old theories of protection to be false. Safe equipment today, thanks to technological progress and thorough testing, can provide modern business with record protection like never before known in the history of civilization.
Selecting the Right Safe is an Important Decision!
The selection of a safe is a more serious obligation than the selection of other types of office equipment. If a chair, desk, or printer does not do what it was supposed to do for the customer, an adjustment is easily made. A replacement or an alteration can be made and the only harm done is a little delay and some annoyance.
But what happens when the selected safe fails to perform satisfactorily? It can only be tested by fire! After the fire, unfortunately, it is too late to make replacements and adjustments. Statistics show that the chances are almost 50-50 that a business will survive a fire!
Any Safe is Safe – Sometimes
Every safe, regardless of whether it has a specific rating or not, and regardless of its age or condition will resist some type of exposure to fire and will protect its contents.
Ordinary steel files will come through some fires satisfactorily. In fact, unprotected records on a shelf or on top of a desk could survive an office fire. The important factors -- how hot a fire and for how long – are the important issues.
Safes Have Certified Security
No firm can afford to test its own safe equipment in an office fire. Consequently, new models of safe are given extensive tests by manufacturers and by private testing laboratories before they are put on the market. Established safe models are also taken off the regular assembly line periodically and given tests to see that they still conform to their ratings.
The Underwriters Laboratories, sponsored by the National Board of Fire Underwriters, is the primary testing agency. It is chartered as a nonprofit organization for the examination and testing of devices, systems, and materials for safety.
Underwriters Laboratories test the safes supplied to them by manufacturers and authorize the use of a series of labels according to the types of test which the equipment has successfully passed.
Learn More About Burglary Ratings
How to Make a Safe
The modern fire safe depends on a blanket of steam to protect the documents within it. The common insulation elements like glass wool, shiny fooils and the others used in refrigerators, stoves, and home construction give little protection against the intense and prolonged heated developed in a building fire.
The older safes utilized free moisture retained in the cement and water mixture used for insulation. This water evaporated over the years and with it went the potential steam protection. This free water also made damp safe interiors, musty papers and rust. Newer formulas and treatments produce a safe insulation with the water retained in permanent crystalline form. As the heat increases during a fire, these crystals turn to water and then to steam which blankets and cools the interior of the safe.
The insulating element of the safe can be made in either one of two methods. It may be cast in a one-piece, oven-dried monolith, then the metal shell built around it. The second method is to form the metal shell first, then pour the insulation mixture into the shell.
Sudden heat changes during the course of a fire sometimes cause safe to explode. The explosion is caused by an accumulation of hydrogen. In the manufacture of a modern quality safe, provisions are made to eliminate this hazard.
Remember the Date, 1917
It was not until 1917 that safes were given any reasonable tests for protection against fire hazards. The results of the first standardized tests proved that many of the old theories about adequate protection were false. After the test, manufacturers changed construction methods radically.
A massive, heavy safe looks like it can give plenty of protection. But, if it is old, it probably lost all of the fire-protective properties it ever had. If it was made before 1917, it never had some of the protection we consider necessary today!
Most safes made before 1917 we insulated with plain water and cement. When the free water evaporated, there was none left to make the steam blanket which protects the records from heat.
Older safes depended on supporting strength on their outer shells alone or on heavy bands at the front and back. At the comparatively low temperature of 1,000 degrees, this supporting metal lost as much as 70% of its strength. With the support weakened, the safe would warp and allow the heat to enter. Any drop during the course of the fire, of course, would burst the safe and open the contents to flames.
Safe construction methods have changed radically since the test on safes have been conducted scientifically. In the older safes, the heat was rapidly transmitted to the interior of the safe by its metal hinges, spindles and handles. Openings between the door and frame often permitted direct access for the heat of a fire. Solid steel fittings in the door and jamb conducted the heat quickly.
Doors are now tongue and grooved in a design that impedes the path of the heat. Casings for the insulation are of light material and assembly methods are engineered so that there is a minimum of heat penetration to the interior of the safe.
Relocking Devices
Knocking off the combination lock and driving out the spindle was a favorite method of opening a safe at one time. Safes can now be equipped with a relocking device, however, which foils this practice. The relocking mechanism is very sensitive to any tampering with the combination lock and any pounding will immediately deadlock the bolt work of the safe.
A safe having an Underwriters’ Laboratories labeled relocking devise is eligible, under certain conditions, for a reduction in burglary insurance.
There are occasions within the business office where the combination of the safe is known only by one or a few persons, yet a number of employees are required to work with the contents of the safe.
An older method of dealing with this problem is the use of a separate key-locked inner door. Authorized employees are issued keys to the inner door but do not know the combination to the safe. The inner door has dropped in popularity, but it is still available on some safes.
The modern approach to the same problem is locked interior compartments. Employees are issued keys to the compartments they are entitled to enter. An alternative method used on some safe models is a separate key lock in the bolt work of the safe. After the combination is worked, the safe can be opened with a key. Turning the combination dial makes the key inoperative.
WHAT YOU NEED TO KNOW ABOUT THE VALUE OF YOUR RECORDS
Many business people take their record keeping for granted. It is a necessary nuisance. It is not that they think records are not important but too many business people fail to realize that their business records are what keep them in business.
For over 40 centuries, humans have been protecting their personal and valuable possessions in strong boxes. It has been a relentless challenge for the designers and manufacturers of safes to outwit the safe crackers and burglars of the world.
Today, the science of safe and vault makers can provide protection against virtually any conceivable hazard – save perhaps a direct hit from an atomic bomb.
Despite the remarkable advances in the design and production of protection equipment, it is estimated that more than 75% of the equipment in use by businesses today are incapable of protecting the valuables inside the safe. An additional mountain of vital business records has no protection whatsoever!
When Is a Safe NOT a Safe?
There is confusion of terms in the use of fire and theft resisting equipment. This confusion in terms leads many users to believe that they have more protection than they really have. It is natural for customers who have a “safe” to believe that anything they put into it will be “safe.” Our job is to be sure that our customer recognizes the type of protection they are getting with the equipment they purchase.
This is a FIRE safe.
It gives FIRE protection and is engineered and insulated to protect its contents against HEAT. It is NOT designed to keep out an experienced burglar.
This is a BURGLARY RESISTANTsafe.
It is engineered and constructed to protect cash and valuables against experience burglars. It gives little protection against heat.
This is a COMBINATION (COMPOSITE) safeIt gives both burglary and fire protection. The outer material is metal and the inner layer is a special composite material that provides both burglary and fire resistance.
This is an INSULATED VAULT door.
It gives similar protection to that of a fire safe but is somewhat limited in it's degree of burglary protection.
VAULTS
Underwriters Laboratories assigns one of four ratings to vault doors and modular vault panels based on expert burglary attack with cutting torches, fluxing rods, portable electric power tools, portable hydraulic tools and common mechanical tools for a specific time period. UL labels are mounted on the vault door and individual modular vault panels. When the UL rating for the door and panels are different, the overall vault rating is determined by the least burglary resistive component.
The ratings are:
Class
Attack time
M 15 minutes attack time I 30 minutes attack time II 60 minutes attack time III 120 minutes attack time
Vault construction
Vault doors that are not UL-listed are evaluated based on the construction and thickness of the steel incorporated in the door. For non-UL listed vaults or panels, construction of the vault floor, ceiling, and walls is evaluated in terms of their thickness, and construction (steel, masonry, cinder block, filled cinder block, or reinforced concrete). Vaults constructed of poured concrete with reinforcing rods must meet the standards of construction established by the American Society of Testing and Materials to assure appropriate burglary resistant protection, but are not rated by U.L.
Doors and vault construction that are not burglary resistant may be listed as fire resistant and containers with these components should be used for storage of records and other valuable papers. Vaults constructed with masonry block, brick, or steel are not typically acceptable for burglary protection, except when values are low and other burglary protection compensates for the deficiency.
When the electricity fails and phones are out, your safe or vault is your last defense against a burglar.
This page contains excerpts from from the “National Stationery and Office Equipment Association”